Customs clearance process
Dropshipping logistics
e-commerce shipping solutions
Eco-friendly packaging solutions
International shipping guidelines
local freight shipping services
Warehouse management
efficiency, logistics, logistics strategies, logistics success, warehouse best practices, warehouse efficiency, warehouse expert tips, warehouse future trends, warehouse guide, warehouse management, warehouse management 2024, warehouse operational excellence, warehouse operations, warehouse optimization, warehouse strategies, warehouse success tips, warehouse techniques, warehouse tips, warehouse tips 2024, warehouse trends
prraelogistics
1 Comments
Warehouse Management Made Easy: Simple Steps To Success
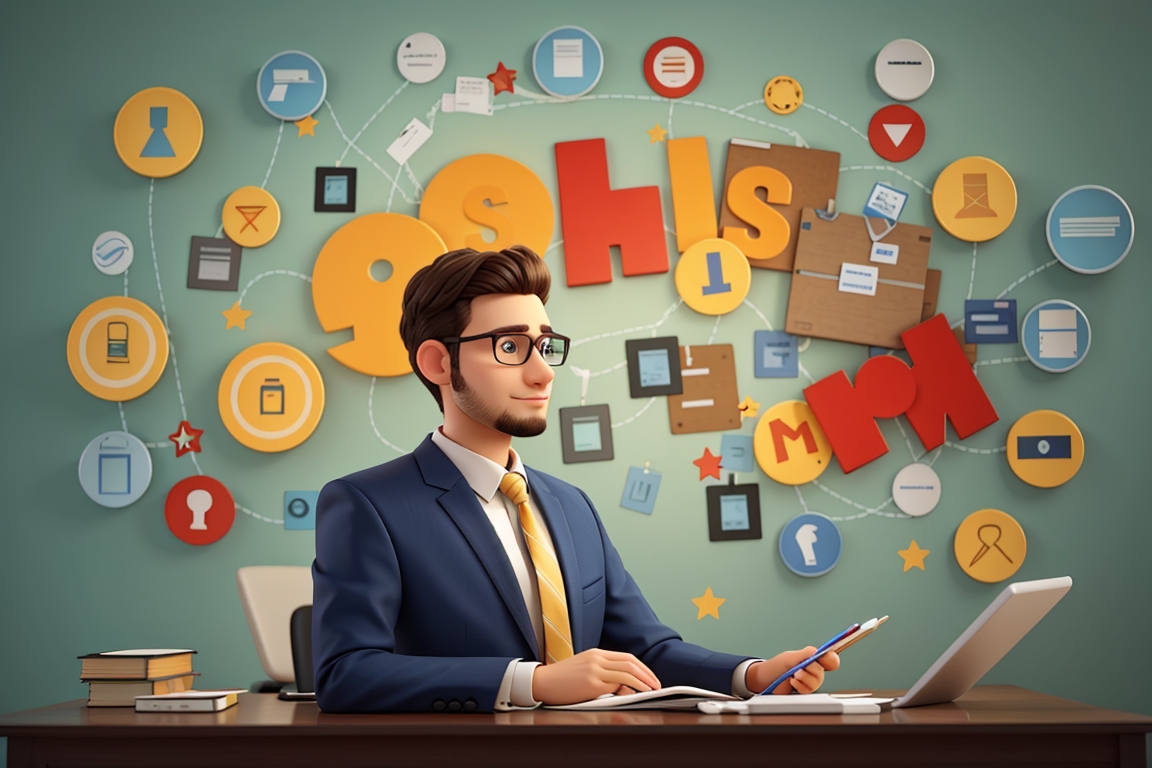
Table of Contents
Warehouse management is the backbone of the logistics and supply chain industry and ensures that goods are stored, tracked, and delivered efficiently.
In today’s fast-paced market, where customer demands for speed and accuracy are high, effective warehouse management can differentiate a business and drive long-term success.
Whether managing a small warehouse or a large distribution center, proper warehouse management impacts every stage of the supply chain, from inventory control to order fulfillment and customer satisfaction.
This blog will explore the key components of warehouse management, common challenges, and best practices to optimize operations.
The Importance of Warehouse Management
Effective warehouse management is critical for several reasons:
Data-Driven Decision Making: Modern warehouse management systems (WMS) offer real-time insights into inventory levels, order status, and warehouse performance, enabling informed decision-making and continuous improvement.
Operational Efficiency: By streamlining processes, businesses can move goods quickly and efficiently, reducing operational costs and increasing productivity.
Inventory Control: Proper warehouse management ensures that stock is accurately accounted for, minimizing overstocking or stockouts and ensuring orders are fulfilled correctly.
Cost Reduction: Efficient warehouse operations help reduce labor costs, improve space utilization, and minimize errors that can lead to costly returns or customer dissatisfaction.
Customer Satisfaction: Quick and accurate order fulfillment directly impacts customer satisfaction, helping businesses retain loyal customers and boost their reputation.
Key Components of Warehouse Management
Warehouse management encompasses a variety of activities, each critical to ensuring smooth operations. Below are the key components:
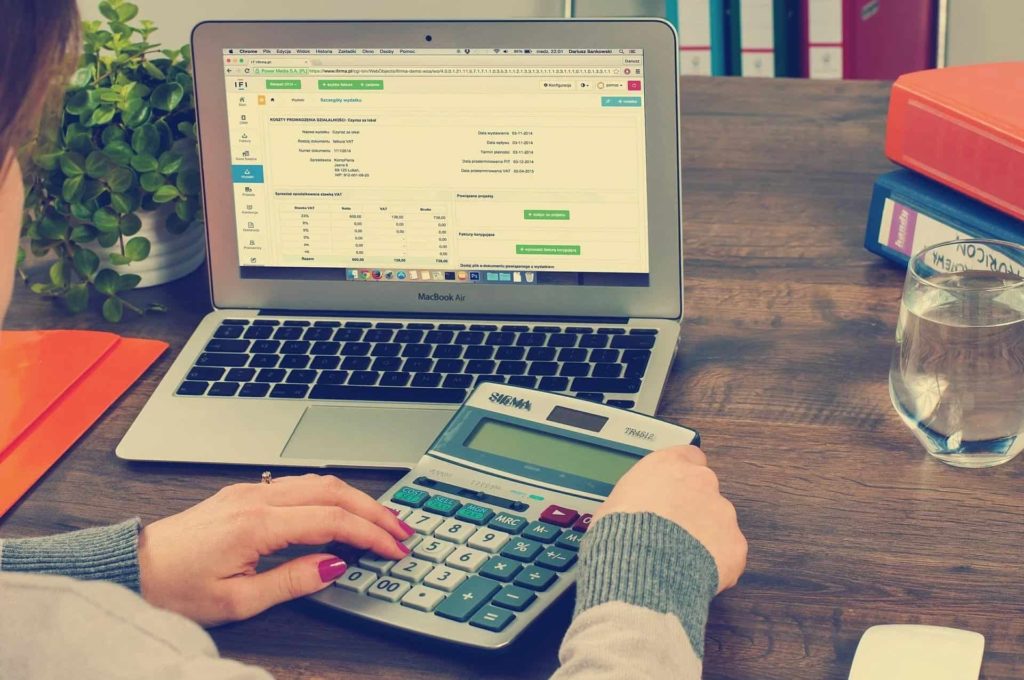
1. Inventory Management
Inventory management is central to warehouse operations. It involves tracking goods as they enter the warehouse, monitoring stock levels, and ensuring that items are stored and picked efficiently. A well-managed inventory ensures that the right products are available when needed without overstocking or running into stockouts.
2. Order Fulfillment
Order fulfillment refers to the process of picking, packing, and shipping customer orders. Efficient order fulfillment relies on accurate inventory records, optimized warehouse layouts, and streamlined picking processes. Ensuring that orders are filled accurately and promptly is critical to maintaining customer satisfaction.
3. Receiving and Putaway
Receiving involves accepting goods from suppliers, verifying the quantity and quality of incoming products, and recording them into the system. Putaway is the process of placing goods in the appropriate storage locations, organized for easy retrieval. Proper receiving and putaway processes are essential to maintaining order and minimizing errors during order fulfillment.
4. Picking and Packing
Picking is the process of retrieving goods from storage to fulfill customer orders. Packing ensures that the picked items are properly prepared for shipment. Optimizing these processes with techniques like batch picking, zone picking, or wave picking can significantly reduce labor costs and improve efficiency.
5. Warehouse Layout Design
The layout of a warehouse plays a significant role in operational efficiency. A well-designed layout ensures that frequently picked items are easily accessible, minimizes the time spent walking between different areas of the warehouse, and maximizes space utilization.
6. Shipping and Delivery
Once orders are packed, shipping ensures that they are dispatched to the appropriate carrier for delivery to customers. An effective shipping process requires coordination with transport providers, efficient labeling, and tracking to ensure that orders reach customers on time.
Â
7. Safety and Compliance
Warehouse management also involves maintaining a safe working environment and adhering to industry regulations and standards. This includes proper training for staff, safety protocols, and regular inspections to ensure the warehouse operates within compliance standards.
8. Technology Integration
Modern warehouses are increasingly reliant on technology to streamline operations. Warehouse management systems (WMS), barcode scanners, radio-frequency identification (RFID) technology, and automation are some of the tools that improve accuracy, efficiency, and data visibility.
Â
Common Challenges in Warehouse Management
Despite its importance, many businesses face challenges in managing their warehouses effectively:
Technology Adoption: Smaller or traditional warehouses may struggle to adopt and implement modern technology solutions, limiting their ability to compete with more advanced competitors.
Inventory Inaccuracy: Poor inventory tracking can lead to stock discrepancies, overstocking, or stockouts, all of which impact order fulfillment and customer satisfaction.
Inefficient Layouts: A poorly designed warehouse layout can lead to longer picking times, increased labor costs, and operational inefficiencies.
High Labor Costs: Labor is often one of the largest expenses in warehouse operations. Inefficient processes, manual data entry, and poor inventory organization can lead to higher labor costs.
Space Utilization: Ineffective use of available warehouse space can lead to overcrowding or underutilization, increasing storage costs.
Order Fulfillment Errors: Errors in picking, packing, and shipping orders can result in returns, customer dissatisfaction, and lost revenue.
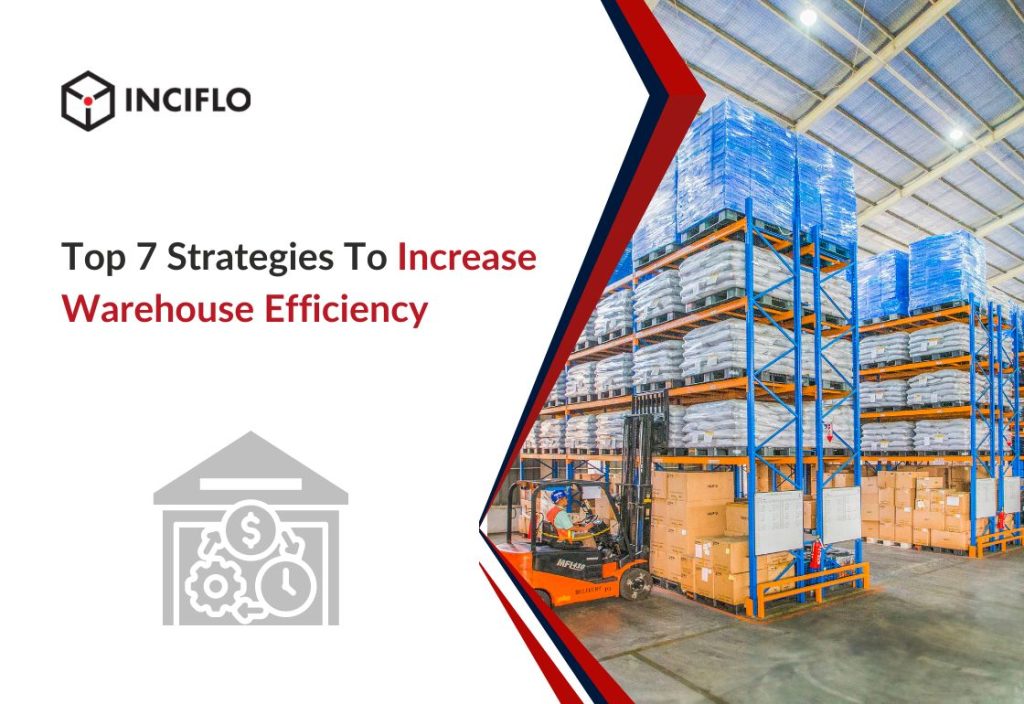
Â
1. Invest in a Warehouse Management System (WMS)
A WMS is a software solution that helps manage and control warehouse operations, from inventory tracking to order fulfillment. Key benefits of a WMS include:
- Real-time inventory visibility
- Automated picking and packing processes
- Integration with other systems, such as ERP and transportation management systems (TMS)
- Reporting and analytics for performance tracking
By leveraging a WMS, businesses can significantly improve accuracy, reduce labor costs, and enhance operational efficiency.
2. Optimize Warehouse Layout
An optimized layout minimizes the time and effort needed to move goods through the warehouse. Consider these strategies:
- ABC Analysis: Arrange items based on their importance or picking frequency. Items with high demand (A-items) should be located near the packing area, while slower-moving products (C-items) can be stored further away.
- Cross Docking: Cross docking eliminates the need for long-term storage by immediately moving incoming goods to outgoing shipment areas, reducing handling time and storage costs.
- Slotting: Slotting organizes products based on size, weight, and picking frequency. Ensure that heavy or large items are stored on lower shelves, while smaller or frequently picked items are stored at accessible heights.
3. Automate Where Possible
Warehouse automation can greatly enhance efficiency by reducing manual tasks, improving accuracy, and speeding up operations. Examples of automation in warehouses include:
- Automated Storage and Retrieval Systems (AS/RS): AS/RS systems automatically retrieve and store goods, reducing human error and minimizing the need for labor.
- Conveyor Systems: Automating the movement of goods within the warehouse reduces manual handling and accelerates order fulfillment.
- Robotic Picking Systems: Robotic systems can assist with picking items, improving speed and accuracy in high-volume warehouses.
4. Implement Inventory Control Techniques
Effective inventory control is key to minimizing stock discrepancies and ensuring accurate order fulfillment. Techniques include:
- Cycle Counting: Regularly count a portion of your inventory to ensure accuracy without needing to shut down operations for a full physical inventory.
- Just-in-Time (JIT) Inventory: JIT minimizes the amount of stock on hand by ordering goods only when needed, reducing holding costs and the risk of obsolescence.
- Safety Stock: Maintain a buffer of safety stock to protect against unexpected spikes in demand or supply chain disruptions.
5. Train Staff and Foster a Culture of Efficiency
Warehouse employees play a vital role in day-to-day operations, and their performance can greatly impact overall efficiency. Invest in regular training for staff on best practices, safety procedures, and the use of technology. Foster a culture of continuous improvement, encouraging employees to provide feedback and suggest ways to streamline processes.
6. Monitor Key Performance Indicators (KPIs)
Tracking KPIs allows businesses to measure warehouse performance and identify areas for improvement. Important KPIs for warehouse management include:
- Order Accuracy Rate: Measures the percentage of orders fulfilled without errors.
- Inventory Turnover Rate: Tracks how quickly inventory is sold and replaced over time.
- Picking Accuracy: Measures the accuracy of the picking process in fulfilling customer orders.
- Order Cycle Time: The time taken from when an order is received to when it is shipped.
By monitoring these KPIs, businesses can assess their warehouse performance and make data-driven decisions to improve operations.
Cracking the Code: How to Find Buyers for Your Export Products in 2024
Tag
efficiency logistics logistics strategies logistics success warehouse best practices warehouse efficiency warehouse expert tips warehouse future trends warehouse guide warehouse management warehouse management 2024 warehouse operational excellence warehouse operations warehouse optimization warehouse strategies warehouse success tips warehouse techniques warehouse tips warehouse tips 2024 warehouse trends
1 comment